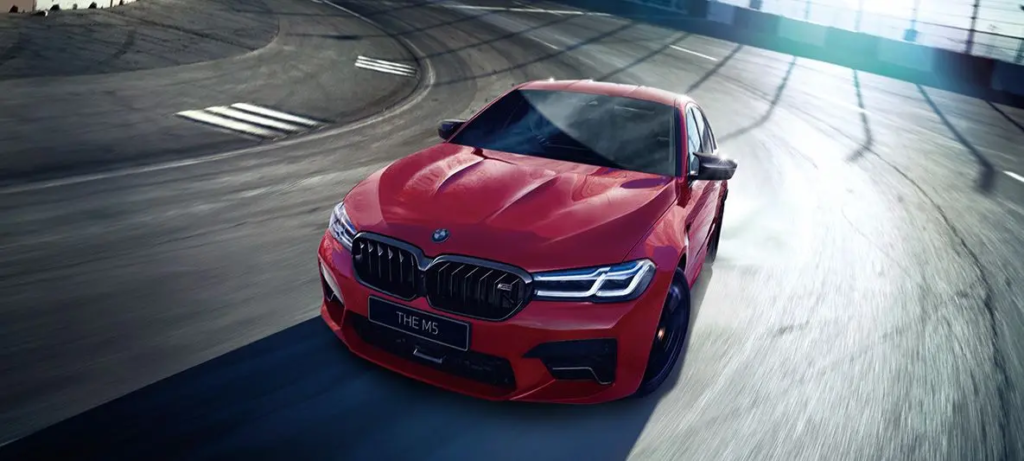
先日、新型「M3」および「M4」が発表されて話題になりましたが、中でも全車にカーボンファイバー製ルーフが標準装備となっていたことに注目を集めました。
カーボンファイバーはボーイング787など、最新鋭の航空機でも利用比率が高まっていますが、クルマの分野ではBMWが積極的に導入を進めています。釣り竿やゴルフクラブ、ロードバイクのフレームなど、私たちの身近にある商品でも採用が増えているカーボンファイバー、すごいのは知っているけれど具体的にはよく知らない、という方もいらっしゃるのでは?今回は先端素材であるカーボンファイバーについて解説するとともに、BMWでの取り組みについても紹介していきます。
軽くて強い!カーボンファイバー
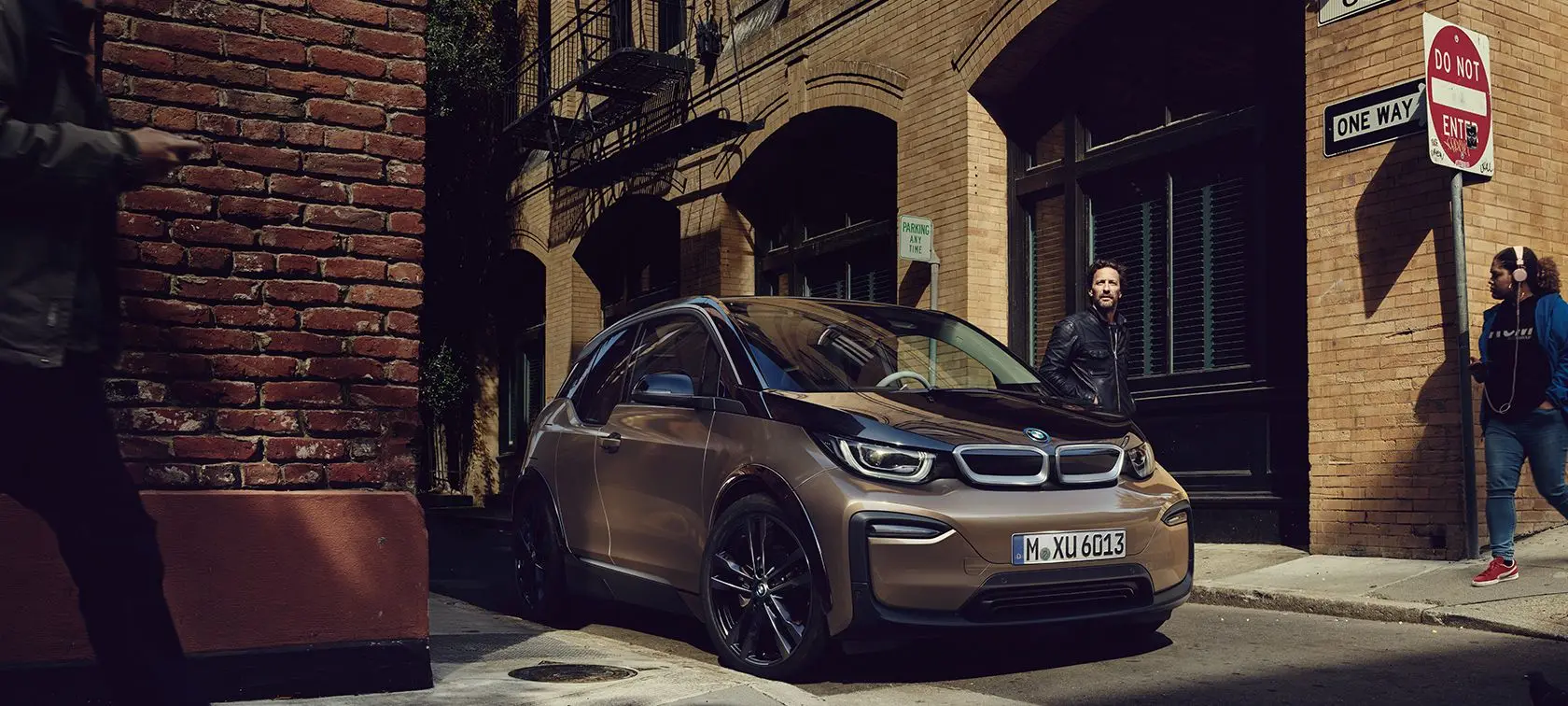
画像引用:https://www.bmw.co.jp)
カーボンファイバーとはその名のとおり炭素(カーボン)からできている繊維(ファイバー)のことです。現在主流となっているのは、衣料の原料となっているアクリル樹脂を繊維化して約1000度の高温で焼いた素材で、「軽くて強い」のが特徴です。一般的にはプラスチックを炭素繊維で強化した「CFRP」(carbon fiber reinforced plasticの略)という形で利用されます。
カーボンファイバーの特長は「軽い」「強い」「錆びない」「電磁波遮蔽性がある」「寸法安定性が良い」「振動減衰性が良い」「疲労特性に優れる」「たわみにくい」などがあります。
どれぐらい強くて軽いかといえば、強度では鉄の約10倍、重量は鉄の約25%と言われており、軽量素材として知られているアルミニウムを遥かに凌ぐ高い強度と軽量化効果が期待できます。クルマの燃費には車体の重量が大きく作用しますが、カーボンファイバーを車体に採用すると、燃費が約40%改善すると言われています 。
また、振動減衰に優れている点も見逃せません。近年、ロードバイク(自転車)のフレームは従来のアルミニウムからカーボンファイバー製が主流になってきましたが、重量だけでなく、路面からの振動をきれいに吸収するために乗り心地が良いことも人気の理由となっています。
こうしたことから様々な分野でカーボンファイバーの採用が増えてきています。私たちの身近なところでは先に挙げた自転車や釣り竿、ゴルフクラブなどが有名です。強さと軽さを重要視する航空機の分野でも利用が進み、旅客機としては最新型となるボーイング787(ドリームライナー)では構造重量の約50%がカーボンファイバーで構成されています。主翼および胴体すべてがカーボンファイバーなので目に見えているボディは、ほぼカーボン製と言っても良いでしょう。
BMW「 i3」は重たいバッテリーを搭載することで車重の面で不利なEVでありながらも1,260kgとほぼ同クラスのコンパクトカー並の車重を実現していますが。これもボディにカーボンファイバーを大胆に使用したことが大きいと言われています。
ネックは高い製造コスト
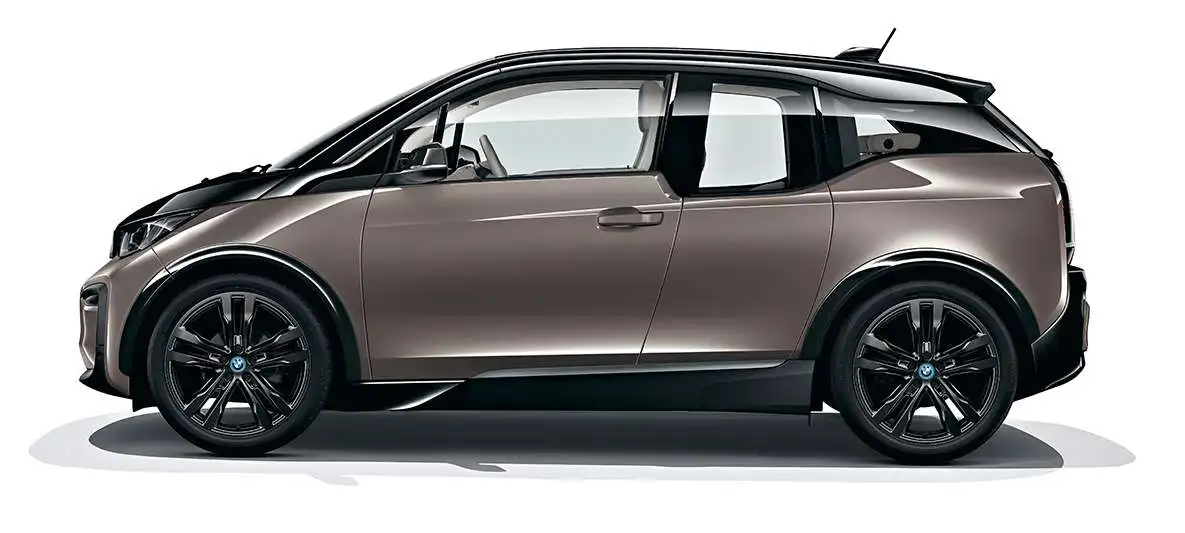
画像引用:https://www.bmw.co.jp
自動車用の素材として、これほど優れた性質を持つカーボンファイバーですが、採用する車種がまだまだ少なく、高級車に限られている起因は高い製造コストにあります。
なぜ、カーボンファイバーは製造コストが高くなってしまうのか、BMW i3の製造工程を例に見てみることにします。
「i3」のカーボンファイバーボディの製造工程
- 三菱ケミカル(旧三菱レイヨン)が繊維素材となるポリ・アクリロ・ニトリル(PAN)を生産
- 米国ワシントン州にあるSGLオートモーティブ・カーボンファイバー社工場でカーボンファイバーを製造
- ドイツのSGL社工場でパーツのもとになるカーボンファイバーの積層板へ加工
- ドイツ バイエルン州のBMWランツフート工場でパーツを成形
- ドイツ ザクセン州のBMWライプツィヒ工場で実車に組みづけ
素材の調達が日本からスタートするのは、カーボンファイバーの生産については日本企業が圧倒的に強いためです。カーボンファイバーの最大手は日本の東レで世界のシェアを3割以上占めています。2位に帝人、3位はSGLカーボン、4位が三菱レイヨンとなっています。
ちなみに、工程2に登場するSGLオートモーティブ・カーボンファイバー社はもともとこのプロジェクトのためにBMWがSGLグループとつくった合弁会社です。この工場への投資額は約1億ドルと言われていることからもBMWのカーボンファイバーにかける意気込みが伝わってきます。なお、この合弁会社についてはSGL社の完全子会社となっていますが、BMWでもSGLカーボンの18.3%の株式を所有しており、カーボン素材の調達にも影響はなく、良好な関係を継続しています。
カーボンファイバーの加工には高度な技術が必要な上に、このように複雑なサプライチェーンを経て組み立てられることからコストはどうしても高くなります。
また、もう1つネックとなっているのがリサイクルの問題です。カーボンファイバーは製造段階でどうしても大量の廃材が発生することや、クルマを最終的に廃棄する際にどう処理するかということが課題です。
とくに「i3」はボディシェルに使用している上、世界で20万台以上も生産(2020年10月時点)されており、年月を経てこれらがいずれ廃車される際には処理しなければならないカーボンファイバーも膨大な量になります。
BMWではカーボンファイバーをリサイクルする技術の開発のために、なんと航空機メーカーであるボーイング社と共同研究を行うことを発表 しています。実は航空機メーカーも機体に利用するカーボンファイバーの使用量が年々増大し、その部品も大型化していることからリサイクルに本腰を入れる必要があるという共通の問題を抱えていたのです。
BMWではボーイング社との共同研究を通じて、航空業界と自動車業界両者のノウハウを融合することでカーボンファイバーを使ったサステイナブルな生産が実現できるようになるとコメントしています。ボーイング社も、今回の合意によりカーボンファイバーの利用および最終用途を促進・開拓する上で極めて重要な一歩になるとコメント しており、両社の強い意志を感じさせます。
カーボンファイバーも素材である以上、それを使って製造された製品は最終的には安全に、環境に負荷を与えずに廃棄するための計画を策定しておく必要があります。例えばリサイクルによって、新しい製品に再利用する方法を検討することは現代の企業に与えられた当然のミッションです。この両社の提携は、社会的にも非常に意義のあるものだと言えるのではないでしょうか。
BMWではカーボンファイバーをこんな風に利用している
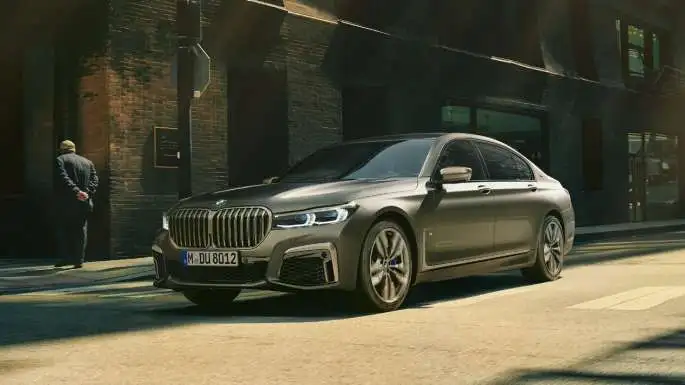
画像引用:https://www.bmw.co.jp
新型「M3」と「M4」では先にデビューしたM5と同様にカーボンファイバー製のルーフが用意されています。スポーツモデルでは重心が低いほうがコーナーでの姿勢が安定しますが、車高を下げるのにはやはり限界があります。ルーフを重いスチールから軽量なカーボンファイバーに替えることで車高を下げるのと同じような効果を得ることができます。
同じくMモデルではカーボンとセラミックの複合材を使用したカーボンセラミックブレーキも用意されています。サーキット走行などハードな環境ではブレーキにかかる負担も相当なものがあります。ディスクブレーキの性能向上のためにはディスクパッドの「食いつき」を高めるとともに、ディスクローターを大型化して冷却効率を高める必要がありますが、通常の鋳鉄ローターだと大型化による重量増は避けられません。
とくに、操縦性に大きな影響を与える、いわゆるバネ下はなるべく軽くして、しなやかに動くようにしておきたい―そんな相反する要求をかなえる解決策がディスクローターにカーボンセラミックを使用したカーボンセラミックブレーキです。
カーボンセラミックは素材的に熱に強い特性を持っていて、しかも鋳鉄ローターのおおむね半分程度の重量に収めることができます。その軽さを活かしてディスク径を大きくできるので、さらに耐フェード性を高めることができます 。
i3で培った技術を活かし、ボディ本体にカーボンファイバーを利用する車種も登場しています。BMW 7シリーズではカーボンファイバー、アルミニウム、ハイテンションスチールといった最新素材を複合して仕上げた革新的な「カーボン・コア」というボディ構造を採用するなど、先代に比べ約130kgという大幅な軽量化を達成 しています。
安全装備や快適装備など現代のクルマに要求される内容はどんどん高度化しています。そのため、そのままだとどんどん重量増が進む一方で、年々厳しくなる環境基準や燃費性能に対応するためには軽量化も同時に進めていく必要があります。フラッグシップの7シリーズで考案されたこの「カーボン・コア」というコンセプトは今後、他の車種にも拡大されていくのかもしれません。
BMWはカーボンファイバーに未来を見る!
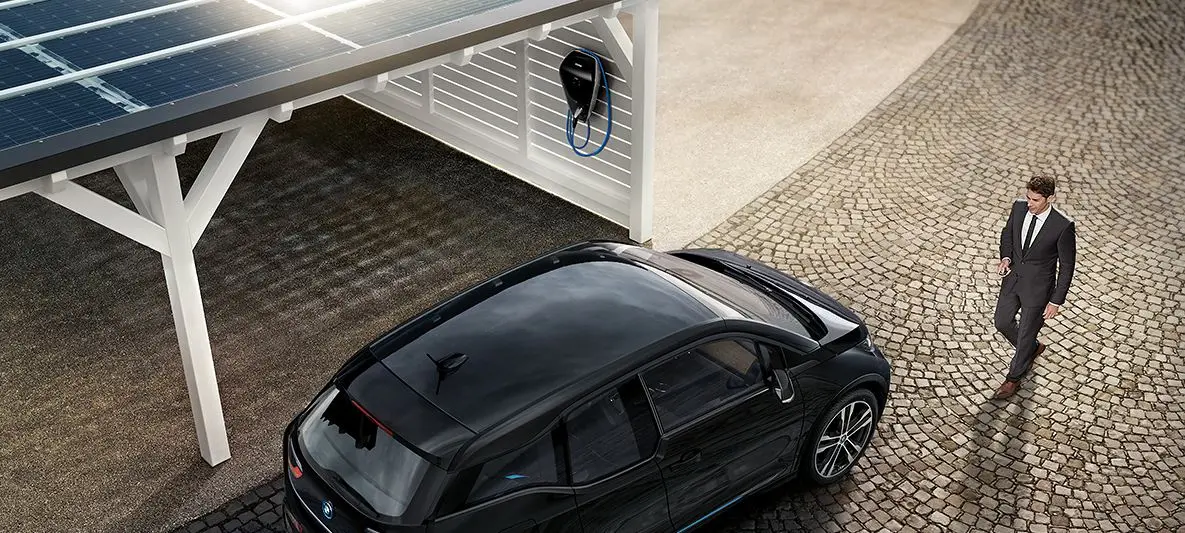
画像引用:https://www.bmw.co.jp
鉄の歴史は古く、紀元前3500年には人類による利用が始まっていたと言われています。クルマの素材としては比較的新しいと言われるアルミニウムについても製錬が始まったのは19世紀と100年以上の歴史があり、日本でも1936年には超々ジュラルミンと呼ばれるアルミニウム合金を開発 、有名な零戦(零式艦上戦闘機)の機体にもすでに利用されていました。
それに比べれば、カーボンファイバーが本格的に製品に利用されるようになったのはごくごく最近のことなのです。
BMWは「i3」で多大な投資を行い、いち早くカーボンファイバーの量産という難しい課題に取り組みました。今後、カーボンファイバーが他のBMW車に拡大していくことを考えると非常に先進的な取り組みだったと言えるでしょう。
ネックとなっているコストの高さや加工の難しさ、リサイクルの問題などにもBMWでは今後も新しい解決方法をどんどん見いだしていくのではないでしょうか。